The world’s largest metal 3D printers are operating in a massive Long Beach factory, printing Relativity Space’s reusable Terran R rocket, the company announced this week.
The Long Beach-based space firm unveiled its Stargate 4th Generation printer, which defies conventional 3D printing methods by moving horizontally, rather than vertically, as it feeds multiple wires into a single print head.
Relativity has beaten its own record with this latest generation, as the company has long been home to the world’s largest 3D printers.
“Iteration empowers innovation not only in our rocket design, but also in our own Stargate printers,” Scott Van Vliet, senior vice president of software engineering at Relativity, said in a statement. “In its short history, Relativity has made great strides in evolving its core 3D printing technology, but Stargate 4th Generation printers are our most innovative leap yet.”
The first, second and third generation Stargate printers already operate at speeds faster than the industry standard, the company stated. The new model, however, prints up to seven to 12 times faster.
In addition to increased speed, the new printer also can manufacture objects that are 55 times larger than the third generation model. Thanks to its horizontal orientation, Stargate 4th Generation printers are capable of printing objects up to 120 feet long and 24 feet wide, according to the announcement.
“Stargate printers are designed to unlock rapid iteration, which opens up opportunities for innovation in large-scale manufacturing products,” co-founder and CEO Tim Ellis said in a statement. “What would take traditional aerospace and space manufacturers years to develop and build, will be reduced down to months due to a highly adaptable, scalable, and automated process, made possible through software-driven manufacturing.”
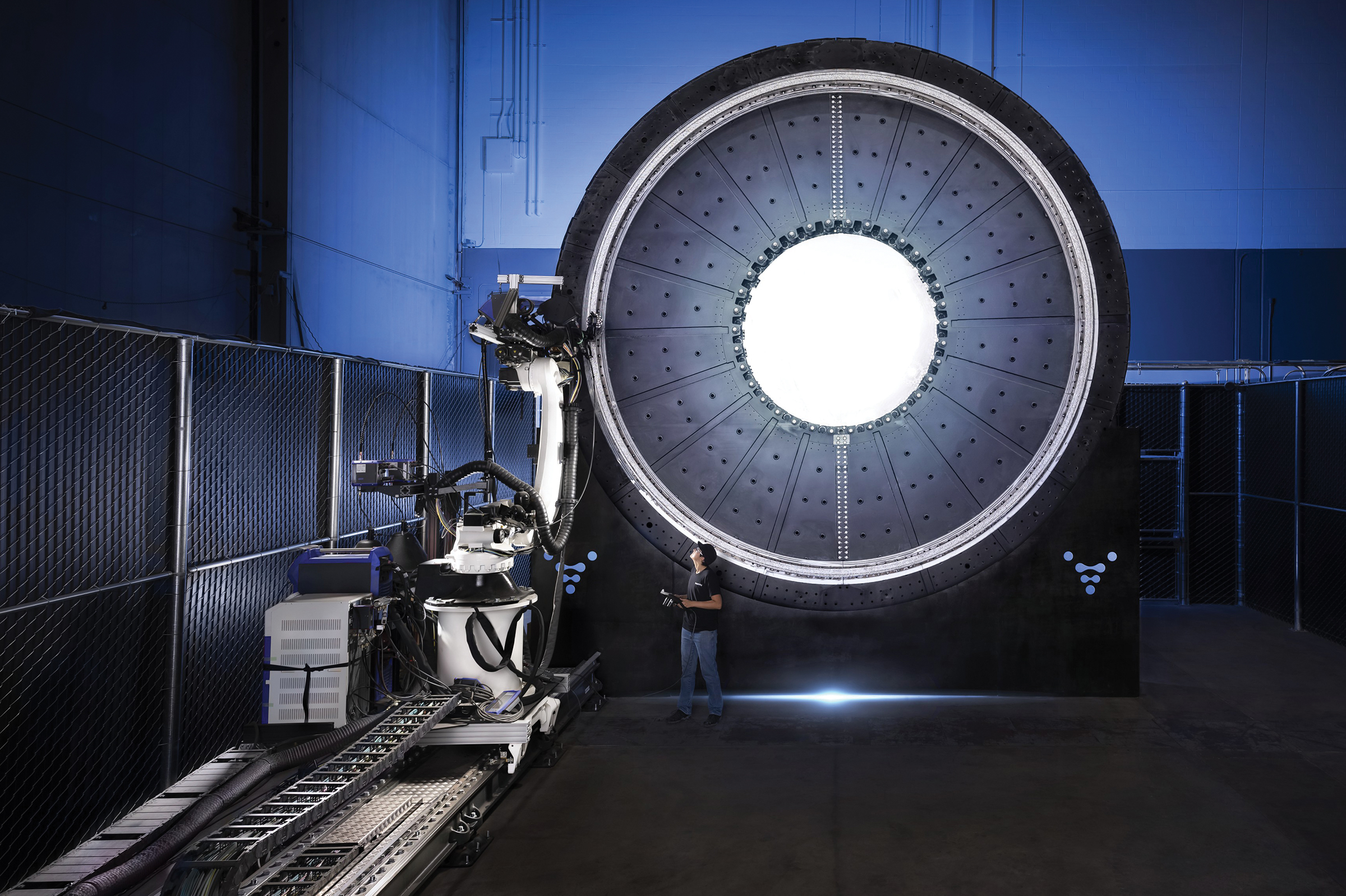
By 3D printing its rockets entirely, Relativity Space produces rockets with 100 times fewer parts faster than traditional rocket building.
Relativity is developing customized software and machine learning techniques that will allow the new printers to produce more complex and even larger metal products at faster speeds with more reliability, which reduces cost, the company stated.
The new printer will support the development and production rate of the company’s Terran R rocket, its first fully reusable spacecraft that will be capable of launching 20,000 kilograms to low Earth orbit. The company already has secured $1.2 billion across five customer contracts for the Terran R, including a multi-launch agreement with OneWeb and a commercial mission to Mars with Impulse Space.
The majority of Terran R components will be printed in Relativity’s new 1 million-square-foot headquarters at the former Boeing C-17 manufacturing plant, which has been dubbed The Wormhole. The Aeon R engines will continue to be produced at the company’s other Long Beach facility, The Portal, on Redondo Avenue.
The company said it plans to have more than a dozen Stargate 4th Generation printers at The Wormhole, each capable of manufacturing four Terran R rockets per year at full capacity. The site is currently 33% operational.
In the long term, Relativity stated that the new printer offers “value-generating potential” for other products within the more than $1 trillion aerospace, aviation, energy and defense industries.
“The compounding rate of progress is high, and we are still in the early days of what printing can achieve,” Ellis said. “We see 3D printing as an automation technology that has the power to change the pace of innovation in manufacturing, which is why we’ve invested in building our own proprietary tech stack from day one.”
Construction continues for Relativity Space in former C-17 site